Ordering and Management
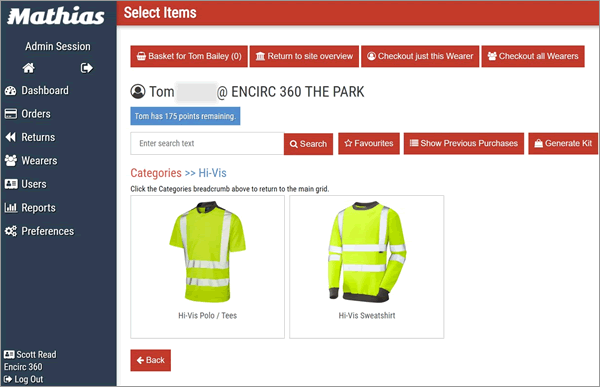
We specialise in developing bespoke workwear and PPE ordering and management solutions for our customers.
We take a consultative approach, and take time to listen and engage with your stakeholders to develop an optimised IT solution.
There are many benefits to this process, which include:
- Reduced administrative time spent placing orders, managing costs and allocation of workwear and PPE orders, raising Purchase Orders, and approving invoices
- Reduced cost – proactively manage spend at point of order
- Increased health and safety compliance – ensure your employees are provided with approved PPE and workwear according to their job role and site
- Improved employee experience – introduce choice and empower your staff
Our industry-leading workwear ordering platform, MUMS, was launched way back in 2003, and since then has evolved to become the most powerful and customizable workwear ordering platform in the UK.
Some of the features of MUMS include:
- Optional employee self-ordering with built-in controls
- Optional job-specific product range
- Optional ordering restrictions at product or basket level
- Optional automated approvals for order requests above agreed limits
- Bespoke product range – eliminate spend on non-approved products
- Full SLA reporting suite in real-time
- Customisable ordering screen – choose your product categories, heirarchy, product descriptions and images
- Bespoke ordering video tutorials
- Optional P2P solutions
- IT integration e.g. SAP Ariba, Single Sign-on
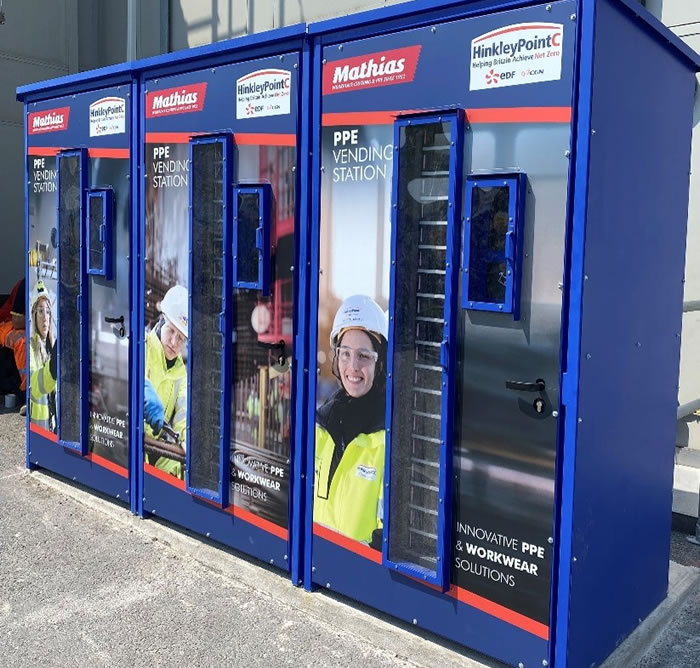
We also have a range of workwear and PPE inventory management solutions that we can provide, including PPE vending, and we have adapted MUMS to enable stock inventory management for your sites, including automated re-ordering.
In addition to this, we provide our customers with a dedicated account manager, who serves as a single point of contact. Our account managers are highly trained, and have extensive knowledge of our customers specific requirements and products, and can also offer:
- Regular account review meetings, to present updates on SLA’s
- Analysis of management information to highlight unexpected spend
- Continuous product range development – present new and innovative products
- Site-based risk assessments and safety audits
- Site-based toolbox talks
- Site-based dynamic foot scanning
- Workwear and PPE stakeholder steering groups